BLOG
7 Things You Should Know About Materials Management in the Digital Era
For many companies, the journey towards a smart factory has mainly focussed on digital networking with external suppliers, business partners and customers. Faster communication and more precise order management are amongst the many benefits they have been enjoying.
Material master data are an essential component of all SAP® logistics processes in companies. Ideally, they are up to date, correct, and reliable. But if they are flawed, it will affect every operating process in your company.
Optimizing SAP master data
For many companies, the journey towards a smart factory has mainly focussed on digital networking with external suppliers, business partners and customers. Faster communication and more precise order management are amongst the many benefits they have been enjoying. With the arrival of the next wave of Industry 4.0, companies are increasingly concentrating on internal processes. Artificial intelligence and the Internet of Things should enable intelligent, ideally autonomous business processes in the area of production.
We will focus on one area that is often neglected in the discussion about the next development stage of tomorrow’s smart factory: materials management and the quality of master data. We have summarised the seven most important things you should know about materials management in the digital era.
Drivers for Digital Material Master Process in SAP
Master data is basic information about all operationally relevant objects such as customers, suppliers, employees and products. All other data in the company can only be used in a meaningful manner if it is linked to the correct master data. We have learned from experience that unclean master data is one of the primary reasons why digitalization initiatives fail.
Efficient creation, maintenance and administration of material master data
Employees often have to struggle with errors and duplicates, because creation and maintenance in SAP® MM® is elaborate and complicated. A wide variety of data are maintained by different departments, such as Purchasing, Sales, and Dispatching. The countless plant views and input fields are often an unreasonable demand, especially for occasional SAP® users!
1. Nothing Works Without Correct Materials Master Data
Poorly maintained materials master data is not uncommon, but at the same time it is one of the main reasons why digitalisation initiatives fail. Many companies are apparently already aware of this: according to a study conducted by the Business Application Research Center (BARC), data quality and master data management are high on the list of priorities for employees and decision-makers who deal with the topic of data in companies.
Redundant, outdated, and erroneous material master data in the manufacturing industry lead to incorrect deliveries and material shortages, which in turn lead to significant disruptions to business processes in materials management. The result is dissatisfied employees, dissatisfied customers, and superfluous costs.
A solution for your material management: easy Material Management is integrated 100% in SAP® and thus supports the IT platform strategy in reproducing as many company processes as possible in one system: a homogeneous IT and process landscape should minimize technical and organizational problems in interfaces, thus significantly reducing operating costs.
In order to achieve optimum data quality, you should firmly embed data management as a task vital to the success of your corporate strategy. Correct data is not a nice-to-have requirement, but rather a decisive factor for the operational capability and agility of your company in times of digital transformation.
Poorly maintained materials master data is not uncommon – and at the same time it is one of the main reasons why digitalisation initiatives fail.
2. Request Materials: Digital from the Very First Step
It is not surprising that consistently digitalised business processes are still the exception in most companies. In everyday business, rehearsed behaviour patterns and familiar workflows are often characterised by manual workarounds. However, a business process is only truly digital if every single step is carried out without media disruptions from the outset.
The digitalisation of materials management begins with requesting materials. Does one of your engineers often need new materials? If so, then you’ll be familiar with the conventional process – although in many cases this is not even a real process.
The applicant contacts the responsible department by email, telephone or even in-house mail and requests new materials. The amount of time spent coordinating is huge, not to mention the high susceptibility to errors. If you want to avoid media disruptions in materials management, start with the request procedure and provide applicants with a self-explanatory input mask. This means that the initial data is transferred to the central system from the very beginning and can then be monitored and processed from there.
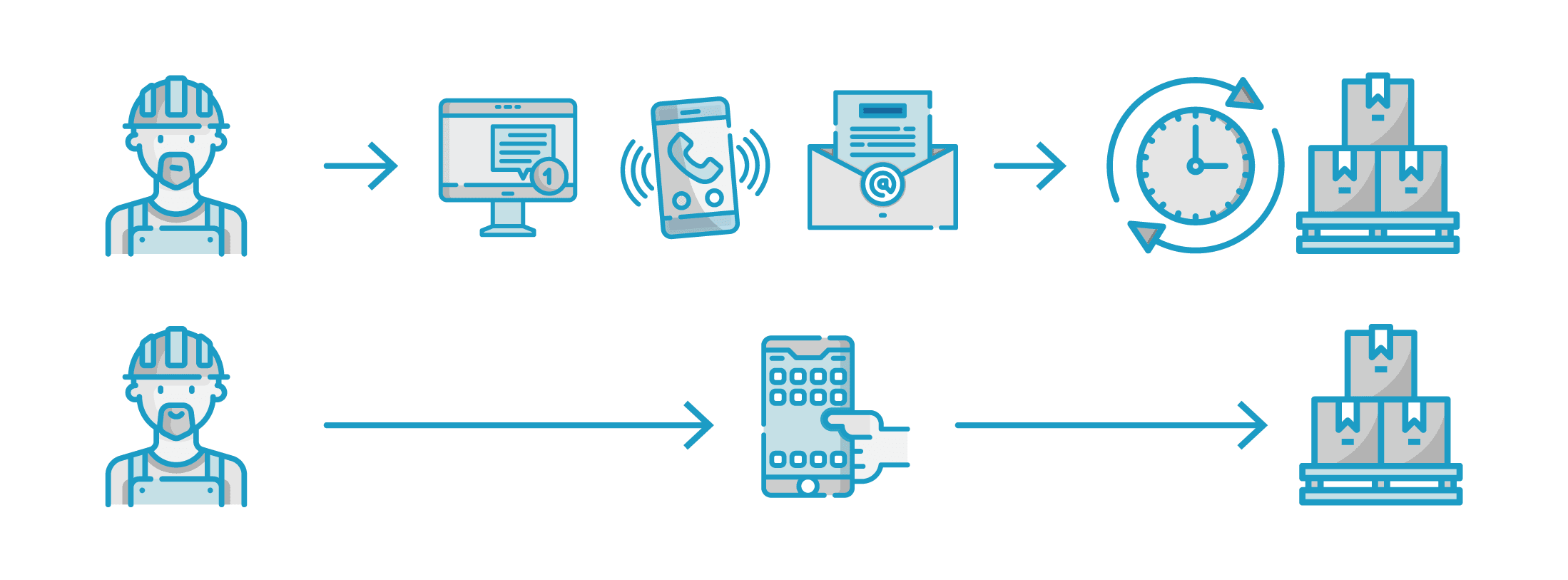
3. Complete Process Transparency Is Only Available Digitally
Requests for materials are followed by process steps such as testing and approval of the materials. Numerous departments of your company are usually involved in this process and this is where it becomes interesting: you can only speak of digitalised materials management if each individual process step is displayed in a transparent, comprehensible and digital way.
Manual processes require a huge amount of coordination. All those involved must be coordinated so that all relevant material views are properly maintained. In addition to the high error susceptibility of manual processes based on emails or paper, there is also the issue that the current status in materials management is often difficult to track.
In the worst case, the entire process comes to a standstill. Long processing times are the result, and in the end hardly anyone knows what the status of the individual process is. Only a completely digitalised process makes materials management transparent and enables continuous monitoring and control of all processes.
4. Get the Most out of Your SAP Investments
Like most companies in the manufacturing industry, you are likely to have invested in IT systems in recent years and decades. With the help of your SAP system, you can control your business processes efficiently and transparently. However, this system can only be fully effective if the underlying database is correct.
In other words, don’t miss the opportunity to get the most out of your IT just because the data doesn’t really work. With the help of an SAP-integrated software solution for setting up the master data, you can accelerate process cycle times, increase master data quality, create better process transparency, reduce error rates and automate many tedious data management tasks.
5. Digital Helpers Support Data Maintenance
Grown ERP systems are often complex and overburden your employees. Occasional users who do not work regularly with the system and are therefore not very familiar with the user interface often take far too long or make mistakes when creating new materials master data.
Automated tools such as our easy materials management solution support your digitalisation process and assist your employees with data maintenance across departments – but there is no magic involved! Thanks to the efficient helpers, you can simply create a clean, correct database without duplicates.
With our easy Material Management for SAP Solutions you receive permanently better data quality. You can shorten cycle times in production and the supply chain in next to no time and gain the transparency you need for your individual role.
- Clean, correct database: All necessary fields are filled
- No duplicates: Only material masters that do not yet exist are created
- Clear responsibilities with data governance: Each department has its own view of maintenance
- Automated processes: Notifications are sent, 360° process transparency
- Control and escalation of material master creation processes
- Full integration in SAP: no further programming knowledge required; access via SAP or Web, available on all mobile devices
- Best practice workflows in one product
Webinar: easy Material Management – Change and create master data
You have recognized that clean material master data leads to success in your company? Now it’ s time to move on to the next steps: The selection of a suitable service provider for the digitalization of your material master creation process.
6. Fully automated material management in a few steps
Request material: An employee – an engineer, for example – requires new material and fills out the basic data 1 & 2. They see only the fields which are important to them in their customized view. If needed, they can attach documents to the request.
Approve material: The master data center receives a “work item,” checks the request, and can return it to the requester if there are errors.
Duplicate check: The system proactively indicates potential duplicates. The material descriptions and drawing numbers are used, among other things, for the check. The check can be individually expanded entirely according to your requirements.

Cross-plant: Basic data, classification data, and document links are created completely automatically for all company’s plants, not just one.
Plant-specific: Different plant views can be defined through a control table, independently of the material type. The system creates the relevant views for the defined plants completely automatically. Individual departments, such as Purchasing or Dispatch, can also be custom controlled to maintain plant views manually.
Material change process: In the material change process in SAP (MM02), existing plant views can be adjusted and new ones can be added. If changes are initiated by employees, they are saved and forwarded in the workflow for approval. In the further course of the process, all participants can see what has been changed and by whom a change was initiated. The entire process of material master maintenance is thus documented and can be traced quickly and easily at any time. The new data is only transferred to the SAP system when the material change process is complete.
7. A Question of Profitability
If you establish order in materials management, you are laying the foundation for the successful digitalisation of all your business processes. The many benefits your company reaps can also be financially substantiated within the framework of an ROI analysis.
Does your company suffer from high indirect process costs caused by many expensive errors in master data maintenance? If so, we estimate that the cost of digitalisation will pay for itself within one year. Other key factors that you should consider when assessing profitability are the number of processes and the number of locations.
For example, a plant manufacturer can quickly create up to 15,000 new material master records per year. If the company has numerous production sites for which different material views have to be created, the process costs for manual processing go through the roof. Here you can achieve a fast ROI through digitalisation.